New instruments created in a Fiji Village
Podcast: Play in new window | Download
Subscribe: Apple Podcasts | RSS
New instruments created in a Fiji Village
Fiji village news starts out as we hear more from Debra Waters and a team of volunteers with the Johken school music department.
View the full images used in this podcast at https://eattmag.com/podcasts/new-instruments-created-in-fiji/
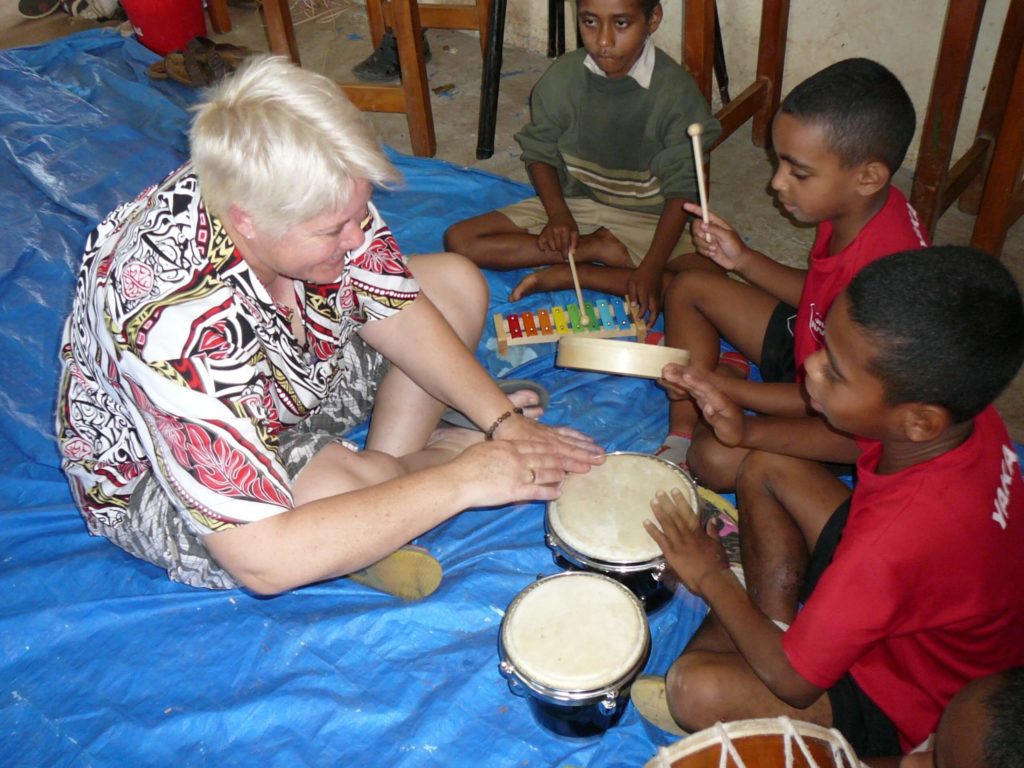
Since Debra and her team has visited several Fiji villages we stop off with her at the Johken school where, over the last couple of visits the school have started a music department.
During previous visits, they also managed to bring over many guitars, bongos, flutes, percussion instruments.
Head teacher Agnes teaching the students with the guitars donated by Debra’s team.
They have also spent three days teaching all the school children’s 274 students from 1st t 6th class how to play the instruments.
Over time the team have been receiving donations to support the school supporting children from Fiji villages near Navua.
On a recent trip up to 100kg of school equipment and medical supplies were delivered to a local small 12-bed hospital in Navua, and the Johken school of over 235 students also in Navua.
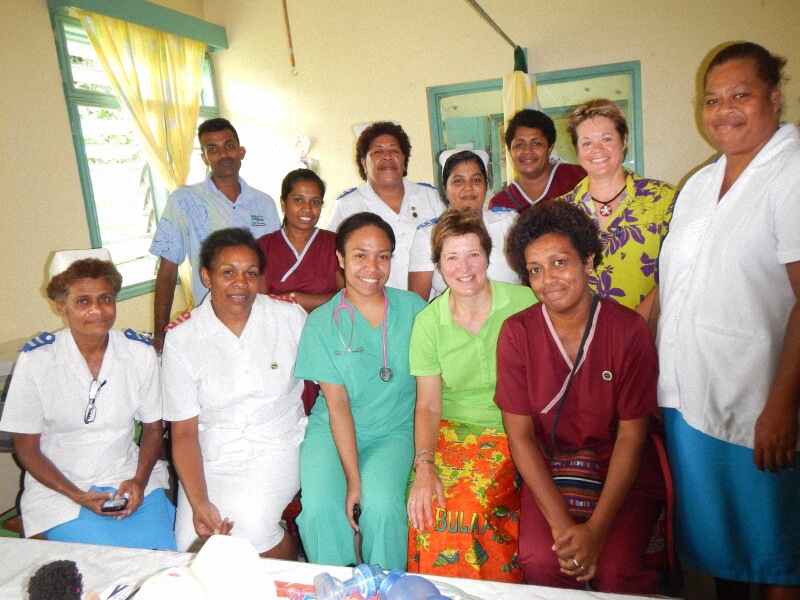
Navua is a small town that floods regularly with the overflow from the Navua river. Apparently, this was the river used to film the blockbuster Anaconda.
A early season downpour meeting high tide can bring floods to this region more recently due to changing weather patterns
During that time the team were also able to learn how Tapa prints made.
The Masi plants used to make Tapa prints grow very well in Vatulele because of the rocky soil, mixed with sand.
The plant is also called the Mulberry plant and can grow up to ten to sixteen foot long. The plant and can also take from six to ten months to fully mature.
The weather is also ideal for growing the Masi ( Mulberry plant) to as the climate is hot on the volcanic island of Vatulele. Masi, as it is known on Vatulele, is also a primary source of income.
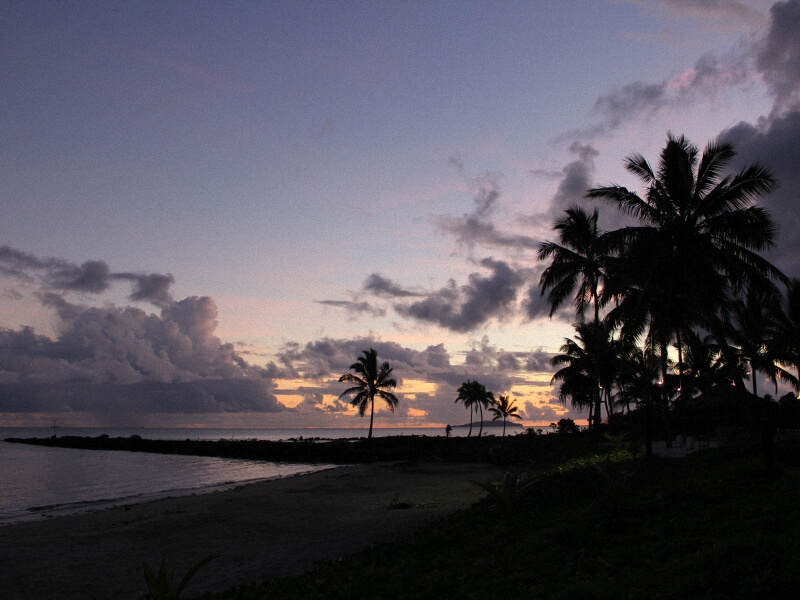
Mostly men from the local Fiji village work in the plantation working on the second stage stripping process. This process involves separating the bark of the mulberry plant from the stem.
The women do mainly separate the bark of the mulberry plant from the stem. They use their feet to hold the stem and use their hands to pull out the bark.
The bark is like a long strip once it is pulled out from the stem.
A third process is used to scrape the bark.
The knife is used to scrap the outer skin of the bark strip to achieve smooth white strips.
The fourth stage is soaking the strips of the bark cloth in water.
Because drinking water is conserved, in Vatulele seawater is used to soak the bark cloth. The strips are then prepared for the beating by soaking them. Soaking achieves a softer texture to the bark strips.
And it can quickly be soaked just a few hours before beating process.
The fifth stage of the beating process
Each strip is beaten up using a wooden mallet, and that is shaped like a flat club.
The strips are laid flat on a long wooden flat log that is carved by men in the village.
Each strip is beaten until it is soft and up to a foot wide.
This process is the most laborious part of beating process known as ” vava ha” to the men of the Fiji village.
The strips of Masi are layered on top of each other using three or four strips until they are about two feet wide.
After that more beating is required until they achieve a six by two feet wide white Tapa to be used for painting.
On an average, this can take a whole day for one woman to beat out a complete piece of six by two-foot tapa.
The sixth stage the drying process is where the tapa is spread out to dry.
The wet tapa cloth is then placed on strips of metal sheets or other flat surfaces as the tapa dries faster on larger surfaces.
The metal sheet sizes ten by two feet are used nowadays because tapa is dried faster and it only takes a few hours for tapa cloth to be completely dry.
The final stage is when tapa is designed using dyes.
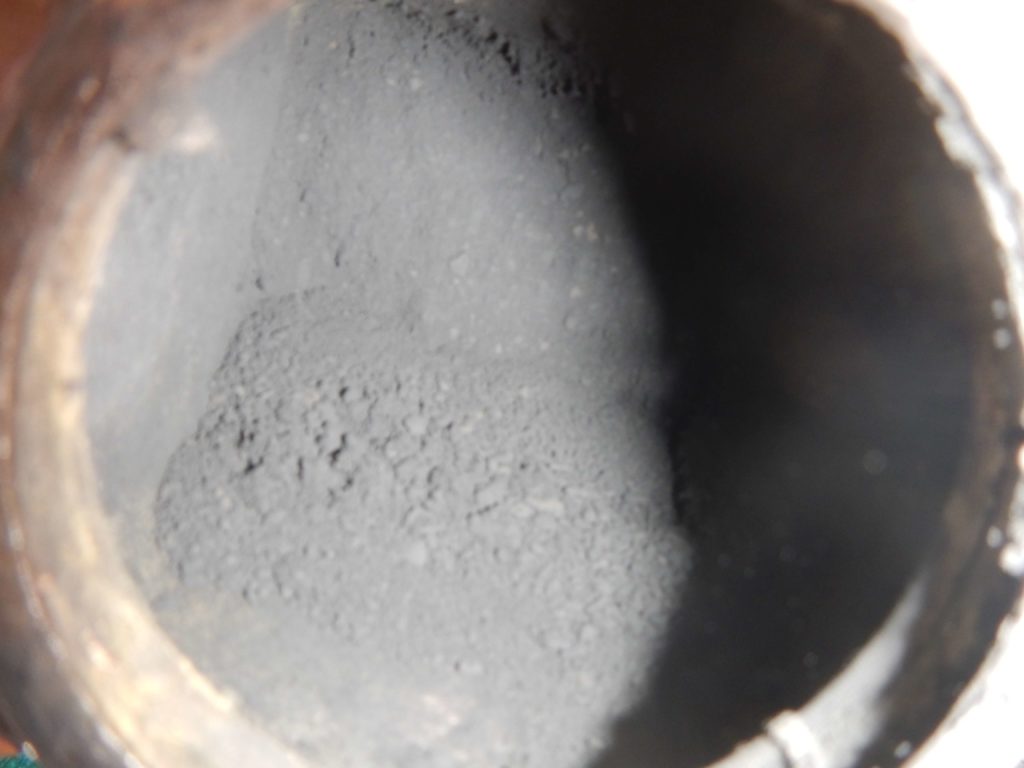
A brown dye is made from the wooden bark of the tree which is soaked and cooked till it’s a thicker texture to become a brown paint or dye.
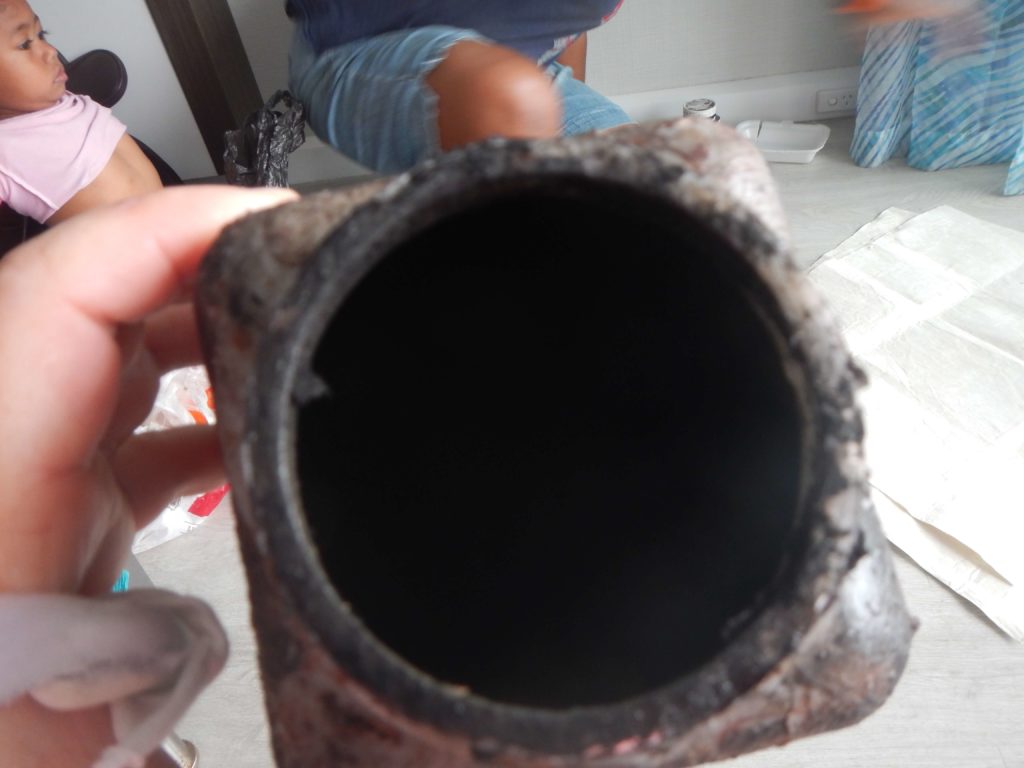
Women designing tapas with the the Masi
The Masi are designed often using designs uniquely from Vatulele island passed down from generation to generation.
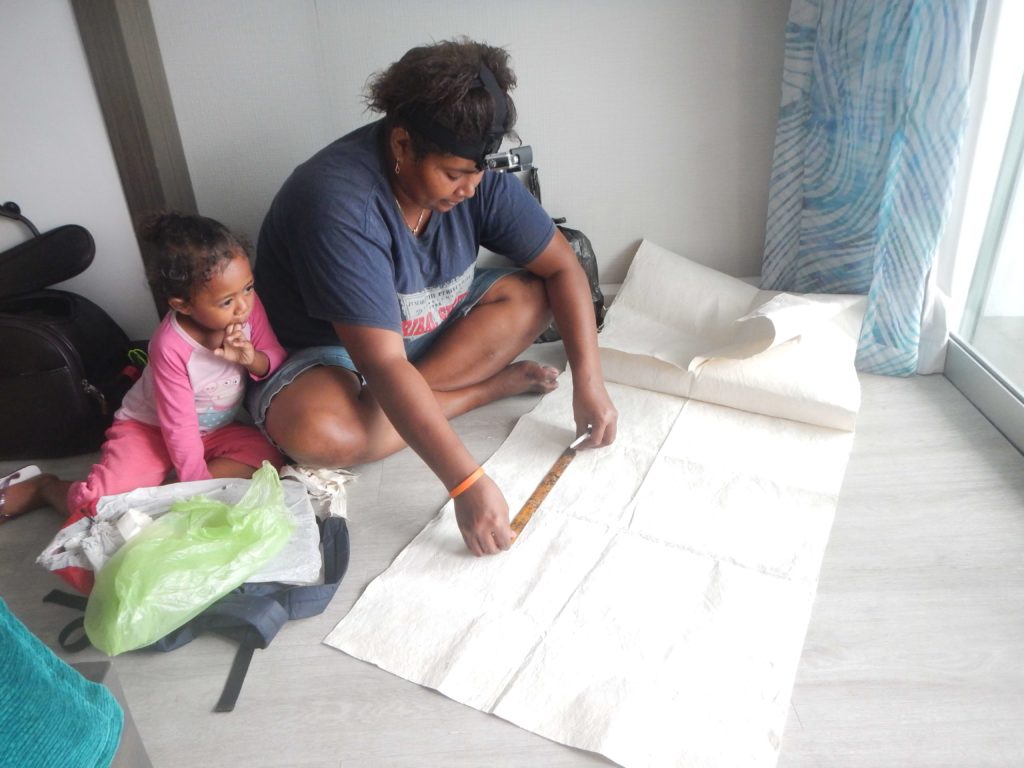
The stencils are cut on X-ray films or cardboard and used to print the designs on tapa cloth.
Tapa is used in Fiji for special occasions identifying with Fijian culture.
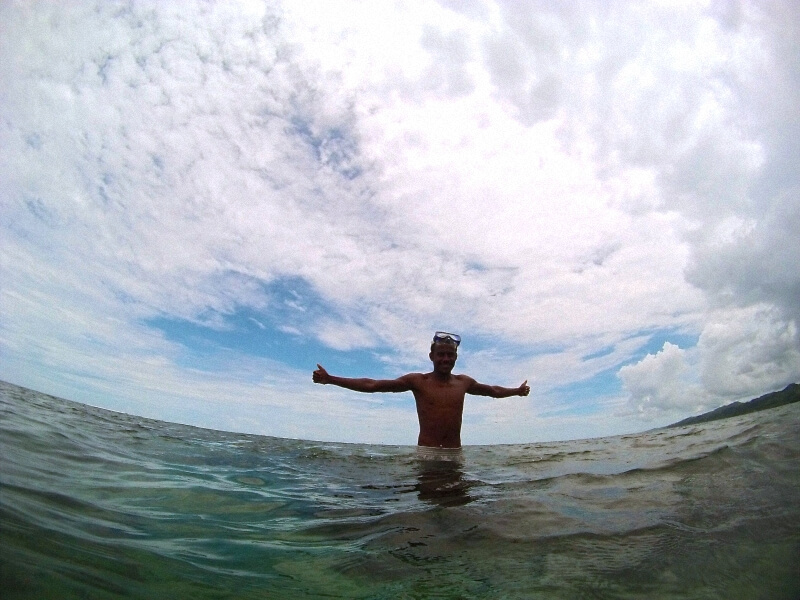
You can contact Debra here https://eattmag.com/marketing-contact/
if you would like to make a donation or support the team in some way.
Subscribe with us on iTunes https://itunes.apple.com/us/podcast/eatt-magazine-podcast/id975085668?mt=2&ign-mpt=uo%3D8
Stay in touch to catch the next podcast and download a bunch of podcasts for your next trip
Learn more about EATT Magazine